Abstract: During the first corrosion inspection of a nuclear power plant, it was found that corrosion occurred on several flange surfaces of seawater pipelines. The structural characteristics of the flange surface of seawater pipelines was analyzed. It is concluded that crevice corrosion occurred due to the inconsistent size of the gasket on the flange surface of the pipeline and the flange sealing surface, as well as the layering between the pipeline coating and the base material of the system. Effective and feasible maintenance measures were put forward to solve the problem of corrosion of flange surfaces.
Overview
The function of the critical water system is to transport the heat load collected by the facility cooling water system to the final heat sink, that is, seawater. Seawater is used to cool the RRI or SEC plate heat exchanger of the RRI system. The
pipeline of the SEC system of a nuclear power unit is made of carbon steel P265GH, 725-H45-ZF101 heavy-duty anti-corrosion paint is adopted for the inner wall. The dry film thickness is 800 μm, and there is current cathodic protection. During the first overhaul of a unit, it was found that the flange surface of some pipelines in the SEC system was seriously corroded. The cause of this problem was analyzed and specific maintenance was conducted.
1.
Reasons for failures of coatings
1.1
An introduction to crevice corrosion mechanism
Crevice corrosion generally occurs in narrow crevices. The width of the crevice must allow the etchant to enter the crevice, and the crevice must be narrow enough to allow the liquid to stagnate in the crevice. Generally, the crevice corrosion happens at the crevice with the most sensitive crevice width of 0.025 to 0.1mm.
Crevice corrosion can be divided into an initial stage and a later stage. In the initial stage, the dissolution of metal and the reduction of oxygen at the cathode to hydroxide ions occur on all surfaces inside and outside the crack:
Anode:
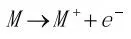
Cathode:
After a short time, the reduction reaction of oxygen would no longer proceed after the oxygen in the seam was consumed. This is because of the lack of oxygen inside the seam and the enrichment of oxygen outside the seam, forming a "differential oxygen supply battery". However, the metal M continued to dissolve in the crevice, and there was an excess of M+ in the solution in the crevice. In order to maintain balance, chloride ions moved to the crevice. At the same time, the cathode process transferred to the outside of the crevice, and hydrolysis occurred for metal salts formed in the crevice, including chloride and sulfuric acid. As a result, the pH in the seam dropped to 2 to 3, which promoted the increase of the metal dissolution rate in the seam; the reduction speed of oxygen also increased, so that the outer surface was cathodically protected, and corrosion of the metal in the seam accelerated. The further excess of metal ions in the crevice made chloride ions get into the crevice, forming metal salts and hydrolysis, increasing the acidity in the crevice, and further promoting the dissolution of metals, which was the autocatalytic process of crevice corrosion development.
1.2
Causes of crevice corrosion of pipeline flanges
1.2.1
Structural characteristics of pipeline flanges
The inner wall of the SEC system pipeline adopted 725-H45-ZF101 heavy-duty anti-corrosion coatings, with a dry film thickness of 800μm. The coating was characterized by being hard and brittle, and the falling was mainly in pieces. The on-site inspection found that the pipeline coating was only applied to the end of the pipeline, and the flange surface had no coating; part of the coating fell off from the substrate, forming a gap. In addition, the flange surface of the pipeline was not completely covered by the gasket, and there was no gasket within the 2cm of the flange surface close to the inner wall of the pipeline.
1.2.2
Cause analysis of crevice corrosion of flanges
According to the principle of crevice corrosion and the characteristics of the SEC system pipeline flange structure, it can be known that crevice corrosion occurred on the flange surface of the SEC system. It can be seen from Figure 2 that two gaps were formed on the flange surface of the pipeline: one was the gap between the coating and the pipeline substrate; the other was the gap between pipelines or the pipeline and the valve flange surface. Therefore, there were also two types of crevice corrosion on the flange surface: one was the corrosion of the base material under the coating at the end of the pipe, as shown in Figure 3 (a) and 3 (b). Only one overhaul cycle, the depth of the corrosion pit reached 11.34mm. The other was the corrosion of the base material on the flange surface, as shown in Figures 3(c) and 3(d); the flange surface showed uniform corrosion, and the depth of the corrosion pit could reach 3.84mm in an overhaul cycle.
Figure 1 Structural characteristics of the flange surface of the SEC system pipeline
Figure 2 Crevice corrosion of pipeline flange surfaces
Figure 3 On-site photos of crevice corrosion of pipeline flanges in SEC systems
2.
Repair measures
Aiming at the corrosion of the flange surface of the seawater system pipeline in the nuclear power plant, Qinshan Nuclear Power used a metal repairing agent to repair the parts with a deep corrosion depth, and then used an anti-corrosion coating to coat the flange surface as a whole to avoid the exposure of the base material and achieve the purpose of protecting the flange surface. The repair effect was good, as shown in Figure 4.
Figure 4 Coating the flange surface
3.
Conclusion
As the cold source system of the nuclear power plant, the seawater system is an important part which can ensure the normal operation of the unit. The corrosion of the flange surface of the seawater system pipeline shows that the design department doesn't consider anti-corrosion in the pipeline design, which brings hidden dangers to the operation of the unit. Therefore, it is necessary to learn from the experience of the operation of the power plant in the future design and installation to avoid the occurrence of similar corrosion.